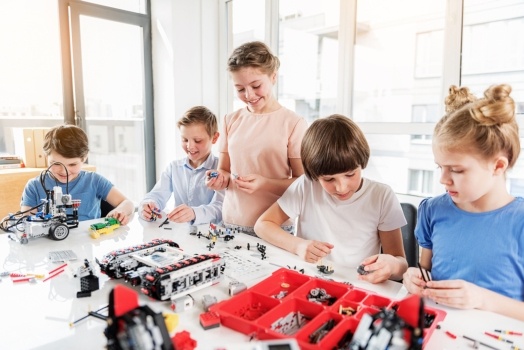
Views: 32
Although Germany is not struggling with a nationwide shortage of skilled workers, many sectors, such as *MINT and healthcare, are vacant. Recruiting skilled workers presents companies with major challenges.
Source Industry of Things by Author / Editor: Nitesh Bansal / Sebastian Human: With the advancement of Industry 4.0, the workforce problem is compounded by the need for specialized manpower, especially in the field of STEM, to accelerate the digitization of industrial production, and thus innovation, competitiveness and growth – not just for business, but ultimately for business Germany as economic power. What makes the situation even more complex: In addition to their expertise, MINT employees must be trained and trained to meet the requirements of a smart factory or factory of the future. Engineer
Skilled labor shortage in Germany
According to recent figures from the Federal Ministry for Economic Affairs and Energy (BMWi), many companies are already acutely affected by a shortage of skilled workers. More than 60 percent even see this as a threat to their business development. The staff shortage also creates great uncertainty among companies when they plan their digital transformation and associated investments – according to the results of the annual business survey conducted by the German Chambers of Industry and Commerce (DIHK).
One reason for this phenomenon is the demographic change and aging of the workforce in industrialized countries. The German economy is losing more people than entering the world of work. An example of the BMWi forecast for Germany: By 2030, the working-age population (20-65 years old) will drop to 45.9 million people – by 2060 this figure will fall even further to 35.7 million. In addition, knowledge is often not documented to the extent required. In particular, this concerns tasks and activities that require a high level of expertise and skills.
Specialize employees
Finding a dedicated workforce can be a big challenge. But given the needs of Industry 4.0, companies also need specialized people who are able to perform certain demanding tasks. This means that companies need to provide targeted and effective training for both the existing workforce and for young professionals entering the labor market. These prepare all involved to do their daily tasks in a complex and technical environment. It is particularly important that training be developed and carried out so that everyone – regardless of the current level of knowledge – can learn and develop. As the industry 4.0 and smart factories continue to evolve, the learning process must be continuous.
How MINT skills have to change
But which skills and expertise does a highly specialized expert, for example an engineer for the factory of the future, need? A recent study by the German Engineering Federation (VDMA) created the profile of an “ideal” engineer of the future based on a survey of industry experts. Currently, engineers are not prepared for digital technological change during their training and need on-the-job training to acquire specific skills and competences. In addition to their more traditional engineering skills, employees must learn industry-specific skills such as automation, sensors, networked production, systems engineering, machine learning, artificial intelligence or robotics from their respective employers.
In an ideal world, this means that companies expect traditional skills combined with specialized skills. Not only the engineer who builds machinery, but also the factory workers and operators of the various machines of the factory of the future must have different capabilities to communicate with robots or co-pots, understand data, use augmented and virtual reality, and provide basic troubleshooting of technology.
In order to further develop Industry 4.0, universities and companies need to work together more closely and ensure interdisciplinary knowledge transfer – theoretical study content must be complemented by hands-on experience, ideally at an early stage.
Industry 4.0 is not a one-man show, but requires collaboration and forward-looking partnerships to ensure that the workers of the future are able and ready for intelligent factories – and thereby drive companies and, in the end, the economy itself.
Related article: Emprego – Trabalhadores sentem-se melhor substituídos por robôs do que por colegas
* MINT = Mathematik (Mathematics) Informatik (Computer Science) Naturwissenschaften (Natural Sciences) Technik (Technology)
Leave a Reply