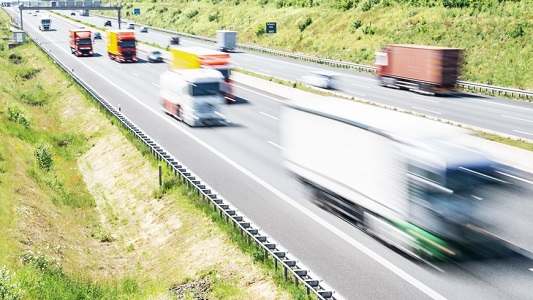
Views: 3
– In the future, commercial vehicles will not only have to emit less CO 2, but also have to meet stricter exhaust emission limits. Many experts hope that this could mean the end of fossil diesel. A possible alternative is dimethyl ether: the highly volatile substance burns very cleanly and can be produced from renewable energy. Empa is investigating this new powertrain concept using a special test engine.
Courtesy EMPA by Rainer Klose: Operating a fleet of trucks is a difficult business. Forget the truck driver’s romance; strong competition and high price pressure is the name of the game. Increasingly stringent environmental regulations aimed at reducing CO 2 emissions and rigid exhaust gas values, especially with regard to nitrogen oxides (NO X), will further intensify the pressure on the industry in the coming years.
If truck operators do not trust the latest technology, they will have to fear increased tolls or tax disadvantages in several countries. Many commercial vehicle manufacturers and operators are now considering alternative powertrain systems to improve the environmental performance of their fleets.
However, electric drives are hardly suitable for commercial vehicles in long-distance operation: the batteries would be too heavy, the charging times too long and the required charging power too high for competitive use.
Hydrogen can solve this problem: in September 2020, the first Hyundai fuel cell trucks are in commercial test operation in Switzerland.
Synthetic natural gas from surplus green electricity is also under investigation: from 2021 onwards, the first natural gas trucks will be refueled on Empa’s mobility demonstrator, move.
But there is another alternative that would be suitable for long-distance transport and that deserves closer examination: In short, dimethyl ether or DME.
Favorable infrastructure, clean combustion
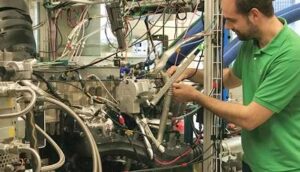
DME is produced on a scale of several tens of thousands of tons annually. The chemical is used as a propellant in spray cans and serves as a refrigerant component in cooling systems.
DME is also widely used as an intermediate product in the chemical industry. Its advantage is that it can be produced at low cost and almost without losses from methanol, which in turn can be produced at low cost using solar and wind electricity. DME therefore offers the opportunity to make trucks CO 2 neutral.
Another advantage: DME has properties similar to those of liquefied petroleum gas (LPG). Unlike hydrogen, it can be transported and stored in standard tanks under low pressure in liquid form.
The technology for LPG filling stations, and therefore also for DME, is economical, is known worldwide and has been in use for decades. Furthermore, as DME contains chemically bound oxygen, the substance burns particularly cleanly and with little soot formation.
Testing on a modified truck engine
There have been tests with DME as a fuel in the past: Volvo Trucks has been conducting field tests with DME-powered experimental trucks in Sweden and the USA since 2013. In Germany, a research project coordinated by the Ford Aachen Research and Innovation Center is running since 2016. The engine was installed and tested on a Ford Mondeo.
Empa, together with FPT Motorenforschung AG Arbon, Politechnico di Milano, the lubricant manufacturer Motorex and other partners, will now extend the knowledge acquired so far. Since the beginning of July 2020, the test engine has been in operation on a dynamometer at Empa’s Automotive Engine Technology Laboratory. The scientists aim to provide solid data on DME’s combustion process, efficiency and environmental impact in the commercial vehicle sector.
“We already know this engine very well,” said project leader Patrik Soltic. “The engine block is derived from a Cursor 11 commercial vehicle engine manufactured by FPT Industrial and has served us for five years in several research projects.
In the past few months, we converted it to DME together with our partner FPT. “That was not easy: in contrast to diesel, the highly volatile DME has almost no lubricating qualities, which would have quickly destroyed the system’s high pressure pump common rail injection.
Operation without fuel additives
Researchers want to test their engine with pure DME, without using lubricant aditives as was done in previous projects. In cooperation with a major European supplier, a new oil-lubricated common rail pump was developed. In addition, the valves and valve seat inserts have been converted into materials suitable for DME. An electrically driven compressor for precise exhaust gas recirculation is also used.
Finally, the combustion chambers and compression ratio of the old diesel engine have also been modified. The new shape of the combustion chambers was developed with the help of mathematical simulations at the Politechnico di Milano. The research project is co-financed by the Swiss Federal Energy Office (FOEN).
Eco-factory fuel
Dimethyl ether (DME), the ecological fuel for compression ignition engines, can be produced from hydrogen and CO 2. If hydrogen is produced with renewable energy and CO 2 is captured from the atmosphere, trucks can be driven with virtually no greenhouse gas emissions.
Empa researcher Andreas Borgschulte and his team are investigating chemical processes that produce DME in the most efficient way possible. The sorption-assisted catalysis method is considered to be very promising: The two gaseous starting materials, hydrogen and CO 2, need to come into contact with active copper particles to initiate the chemical reaction to form methanol or DME.
Water is formed as a by-product. If water is removed from the reaction mixture, the chemical balance changes to the product. In other words: only then can the desired large quantities of methanol and DME be produced. To remove the water, Empa researchers use zeolite, a mineral that absorbs water.
In laboratory experiments, Borgschulte’s team found that, at a certain temperature, CO 2 and hydrogen mainly produce DME, with only a small amount of methanol. “The production of DME using this method is, therefore, theoretically feasible”, says Borgschulte, adding: “Unfortunately, at the moment, the process is still not very efficient”.
The next step would therefore be to refine the chemical process and develop suitable production facilities. Only then can we assess whether DME production using sorption-assisted catalysis is economically competitive. The research was carried out in collaboration with the University of Zurich as part of the LightChEC project.
Simulated road operation
“Now we want to get to know the engine with the new fuel,” says Soltic. The researchers are starting with a style of medium-load driving common on highways, where the engine must deliver 100 kW of power. “Next, we modify the injection time and pressure, among other things, and examine the exhaust emission values and fuel consumption.”
The first results are very promising. The experimental engine works stably in all engine load ranges, practically does not produce soot particles and significantly lower NOx values than a diesel. This leads to a significantly more compact and economical aftertreatment system for exhaust gases, even for future emission limits for extremely rigid pollutants.
The great advantage of the DME operation, says Soltic, is the opportunity to transfer a very high proportion of exhaust gases to the next charge in the cylinder. This is done through the so-called exhaust gas recirculation (EGR).
This technology makes it possible to save a large amount of NOx, which relieves the load on the exhaust gas purification system behind the engine and allows for stricter future limits to be reached easily. With fossil diesel, the high rates of exhaust gas recirculation lead to higher particulate emissions, which is not the case with DME.
During the testing phase, Empa researchers repeatedly collect engine oil samples to track chemical reactions. The results are forwarded to the Motorex project partner, who uses the data to develop a new engine oil specially adapted for DME operation.
Joint research among trucks competitors
“We are currently still in the pre-competitive phase of our research,” explains Soltic. The results of the project are partially public and discussed jointly with competitors in the auto industry.
The platform for these discussions is the “International DME Association” founded in 2001, which currently has 50 members from science and industry. “But at some future stage, everyone will want to keep their results to themselves,” says the Empa researcher. “At this point, it is critical that we have a good knowledge of the technology in order to continue to provide valuable contributions as a research partner to the industry.” Trucks
Related article: Toyota Heavy-Duty Fuel Cell Electric Truck tests