
Views: 28
– Thanks to Neustark’s technology, ETH’s spin-off, concrete recycling plants can store carbon dioxide in the long run.
Courtesy ETH by Ori Schipper: The Neustark pilot plant transforms broken concrete and carbon dioxide (CO 2) into stone granules (Photo: Micha Riechsteiner)
The two young entrepreneurs and founders of the ETH Neustark spin-off work very well together. Johannes Tiefenthaler is a doctoral student in the group of Professor Marco Mazzotti in the Department of Mechanical and Process Engineering, working on the next generation of technology for carbon dioxide mineralization.
Valentin Gutknecht, for his part, is a business economist and deals with the growing team and the operational aspects. They were brought together by their shared vision of implementing a positive business idea for the climate in reality.
Using insights in practice
“There is a lot of research being done on construction-related topics, but the industry has achieved only small reductions in emissions so far, because many of the findings are simply put in a drawer and never used,” says Tiefenthaler. “I would like to use the energy I am investing in my doctorate to make a difference.”
Tiefenthaler had already begun to study several ways to make carbon dioxide react with mineral materials and bind it as limestone during his master’s degree.
There are enough mineral materials on Earth to bind hundreds of billions of tons of carbon dioxide, but since these materials – like magnesium silicate – are not particularly reactive, they need to be heated up to 700 ° C first, says Tiefenthaler. In contrast, the concrete granulate proved to be highly reactive due to the huge total surface area of the numerous particles, each only a few millimeters in size: even without pre-treatment, the broken concrete forms very stable chemical compounds with carbon dioxide .
Refined properties of demolition material
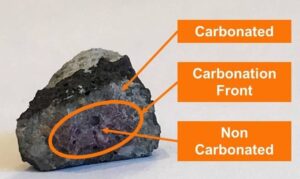
What is particularly special about Neustark technology is that it binds CO² in the pores and on the surface of concrete granules like limestone. This updated granulate can then be mixed with fresh concrete as a substitute for sand and gravel. The updated granulate means that less cement is needed – while the properties remain the same.
“I am very excited that this solution will not be launched in five or ten years – it is available now,” says the second young businessman, economist Valentin Gutknecht. He found time to talk while on his way to the Kästli concrete plant near Bern, where the Neustark pilot plant is gradually being put into operation.
Before founding the company, Gutknecht helped manage the marketing and sales of ETH’s subsidiary, Climeworks, a pioneer in removing carbon dioxide from ambient air. With Neustark, the main challenge is to juggle all the different areas involved, says Gutknecht. They not only need to have control over the properties of the concrete, but also have to navigate the complicated paths of CO² certification.
“We started by interviewing the CEOs of ten different concrete facilities to find out where the problems are,” explains Gutknecht. “Next, we used money from private investors and public funding to develop the first small prototypes.”
They have chosen a container-based solution for now, says Tiefenthaler. In a project supported by the Federal Office for the Environment and the Swiss Climate Foundation, they now aim to demonstrate added value along the entire value creation chain: the plan is for carbon dioxide to come from an energy plant. biogas separation at Arabern wastewater treatment plants in Herrenschwanden. Neustark will then treat the demolished concrete at its pilot plant using this carbon dioxide (liquefied for transportation).
Avoiding emissions – and even reversing them
World cement production releases about four times more carbon dioxide into the air than global air traffic. As Neustark technology helps to reduce the amount of cement needed in construction, it also improves your carbon balance, because some of the emissions from production can be avoided. But Gutknecht and Tiefenthaler highlight an additional aspect: with their trick of capturing carbon dioxide from the air – connecting it to the pores of the concrete granules and connecting it sustainably as limestone – they can even reverse CO² emissions.
“There are very few technical approaches to real negative emissions,” says Tiefenthaler. The use of these approaches has been limited so far, in particular because convincing incentives and business models are lacking. “In this sense, our approach is unique because we show that added value can be created by binding carbon dioxide. And these negative emissions don’t just increase costs – they can really provide economic benefits, ”says Gutknecht.
Other information: Neustark website
Related article: New approach suggests path to emissions-free cement