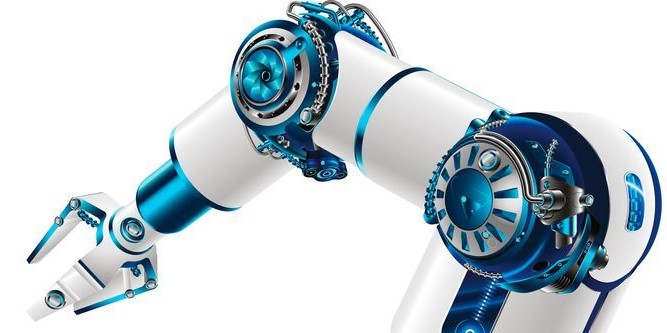
Visitas: 122
Los sistemas robóticos son la tendencia – más y más empresas confían en los ayudantes automatizados. Pero cuando la compra de un robot industrial vale la pena?
Artigo original Elektrotechnik: El sistema de Robot industrial ofrece muchas ventajas para las empresas – que trabajan de forma rápida, confiable y son a prueba de fallos. Pero con un sistema robótico, nuevos costos también llegan a una empresa. Además del costo obvio, hay muchos costos a largo plazo a considerar. Pero cuando vale la pena una empresa utilizar un sistema robótico?
Comprar robots industriales – qué debe ser considerado?
Para entender si la compra realmente vale la pena, es importante comparar toda la fábrica flexible resultante con una producción convencional sin robots. Además de los costos de adquisición del robot, los costos de los equipos periféricos y adaptaciones a las máquinas existentes, así como los costos de instalación, son particularmente importantes para la empresa. Planificación, puesta en marcha, operación, mantenimiento y reparación también cuestan dinero. Los períodos de retorno de los sistemas robóticos son de 3 a 4 años – sólo entonces el nuevo sistema vale la pena.
Economía de sistemas robóticos
Además de los costos directos, los aspectos cualitativos también deben incluirse en la evaluación de un sistema automatizado. El usuario también debe considerar la flexibilidad del robot: no sólo un robot puede ser utilizado para una sola aplicación, pero también se puede utilizar para otras tareas al convertir la producción. La reutilización de un robot y partes de la periferia generalmente reduce significativamente los desembolsos de capital para nuevas instalaciones de producción, de modo que la rentabilidad de los sistemas robóticos en comparación con los sistemas convencionales es a menudo aparente sólo durante un cambio de producción o un cambio de modelo . A continuación, varios métodos de inversión y contabilidad de costes se muestran e ilustran mediante un ejemplo.
¿Cuáles son los costos de los robots?
Como los sistemas robóticos se instalan generalmente en un área de producción, una división de los costos de acuerdo con el área operativa no agrega valor a la comparación de dichos sistemas. Los componentes individuales pueden seguir utilizándose durante un cambio de producto. Así, los costos son relevantes en todo el ciclo de vida y los sistemas pueden ser mejor comparados por una descomposición de los costos de acuerdo con los costos de adquisición, operación y reciclaje. Los tipos de costes individuales pueden entonces subdividirse.
El costo de adquisición: ¿qué cuesta un robot?
Con los costos de adquisición, los componentes individuales se pueden considerar individualmente o se pueden formar grupos de componentes. De esta forma, el costo de los robots puede ser comparado con el costo de los periféricos. Además, el costo de componentes individuales de un sistema de robot, z. Como tecnología de seguridad, sistemas de flujo de material, sensores, efectores finales, enfrentándose unos a otros y así el potencial de optimización pueden ser visibles.
El costo del robot en sí es sólo una pequeña fracción del costo total. Los costos de inversión para el robot son influenciados principalmente por sus características. Estos incluyen capacidad de carga, alcance y precisión. Además, el número de ejes tiene un impacto en el costo de un robot. Las fórmulas detalladas para el cálculo de los costos de adquisición se pueden encontrar en el libro Robótica Industrial, del cual este artículo es extraído.
Los costes operativos
Por un lado, los costos operativos se dividen en costos de mantenimiento de tipos de costo, costos de habitaciones, costos de energía, costos de consumibles y suministros, costos de personal y costos de herramientas. Estos costos son altamente dependientes del proceso de producción y no de las características del sistema. Como resultado, puede ocurrir que los costos operativos varían mucho durante el período de uso. Por otro lado, los costos operativos también incluyen costos de material, configuración, almacenamiento y descarte. Estos son fuertemente dependientes del producto fabricado y, por lo tanto, no se describen en detalle. Sin embargo, deben tenerse en cuenta en el cálculo.
Los costes de mantenimiento planificado incluyen los costos de mantenimiento, inspección y reparación. Se influencian por el tipo, duración y frecuencia de las medidas de mantenimiento. El mantenimiento también influye en la probabilidad de un fallo no planificado de las máquinas. Como resultado, el mantenimiento planificado está sujeto al compromiso entre la alta disponibilidad del sistema y los bajos costos de mantenimiento. Para determinar los costos de mantenimiento, se necesitan índices relevantes para la confiabilidad de los componentes instalados. Para un primer acercamiento, los costos de mantenimiento se pueden calcular por un factor. Un valor típico para los costes de mantenimiento anual es del 10% de los costos de adquisición del sistema.
Los costos de la sala se ve muy influenciados por el diseño del sistema del robot y los requisitos de espacio necesarios. El requisito de espacio es definido por el dispositivo de manipulación y su alcance y el espacio necesario para los periféricos necesarios. Al conectar el efector final al robot, su espacio de trabajo cae en el del robot. El flujo de material y la estrategia de implantación y el equipo necesario tienen un gran impacto en los requisitos de espacio. Si el sistema del robot está rodeado por una cerca de protección, el área dentro de esa cerca se puede utilizar para el requisito de espacio necesario. Sin embargo, los periféricos situados fuera de esa área no deben ser descuidados.
Los costos de energía de un sistema robótico incluyen los costos de electricidad y aire comprimido y están influenciados por el consumo de energía de los componentes individuales del sistema y sus vidas útiles. Los costes de energía no son constantes a lo largo de la vida útil. Los principales consumidores de electricidad de un sistema automatizado son robots y controles, así como equipos relacionados con la aplicación, por ejemplo, cuando suelta la mesa de soldadura, fuente de alimentación de soldadura o transformador y el láser. En la práctica, el consumo de energía del robot depende del tamaño, el alcance, la carga, la aceleración y la velocidad de desplazamiento.
Los costos de consumibles y suministros resultan de la eficiencia de los respectivos componentes y procesos en la tarea de producción. Cuando el gas soldado arco de metal de soldadura es principalmente el consumo de gas inerte y alambre de soldadura para llamar. El consumo de agua de enfriamiento se puede omitir con sistemas de reciclaje apropiados. Para la limpieza de las boquillas del quemador, es necesario un agente desmoldante.
Los costes de personal dependen, por una parte, del número de empleados necesarios y de su nivel de formación y, por otra, del tiempo de trabajo. Los costos se refieren a todo el sistema del robot y no a componentes individuales. Los costos de personal se dividen principalmente en las dos áreas de programación y operación. Los sistemas altamente automatizados no requieren personal operativo. Sólo necesita estar presente para algunos empleados de las fábricas que pueden intervenir en caso de fallo. En sistemas semi-automatizados, sin embargo, los empleados deben ser usados, el z. B. proporcionar el robot con partes individuales.
Los costos de las herramientas son especialmente incurridos en las aplicaciones en las que un proceso de fabricación se realiza utilizando el robot. La soldadura requiere una variedad de boquillas de soldadura o electrodos. Al fresar con el robot, las herramientas de fresado – como con una máquina herramienta – deben ser reemplazadas después de atingir un límite de desgaste. Con garras de garras paralelas, no hay costos de herramienta además de los costos de adquisición. Con ventosas, puede ser necesario sustituir las ventosas individuales.
Los costes de recuperación
La fase de recuperación se divide en las dos áreas de venta del sistema o recuperación en forma de reciclaje o descarte. La flexibilidad del sistema influye en el valor residual. Cuanto más flexible sea un sistema, mayor será el valor residual de la compra. Como un sistema más flexible también implica costos iniciales más elevados, los costos de explotación se pueden calcular como un porcentaje de los costos de adquisición. Las horas de funcionamiento del sistema también influyen en el valor residual. El costo de desmantelamiento de la planta también debe ser considerado. Al descartar el sistema, dos categorías se distinguen. Por un lado, hay chatarra metálica que puede ser vendida. Esto crea una entrada. Por otro lado, la chatarra es producida, que debe ser descartada por una tasa.
Ejemplo práctico: cómo calcular la rentabilidad de los robots
Como parte de una tesis de maestría, varias etapas de expansión para el bloque de células y el montaje de módulos se desarrollaron y compararon económicamente. A continuación, el sistema desarrollado para el nivel básico será comparado con el sistema de la primera etapa de desarrollo, con base en los costos de montaje y en el tiempo de retorno.
En la etapa básica del sistema, 1000 módulos y, por lo tanto, se fabricarán 8000 bloques de células y, en la primera etapa, se producirán 4000 módulos o 32.000 bloques de células. Los costes finales de montaje – sin el material necesario para la producción – deben ser de € 240 por módulo. El tiempo de funcionamiento del sistema es de 20 años. Los índices de la tabla adyacente también sirven como datos de entrada para el cálculo de los costos de montaje y del período de amortización.
Nivel básico: sistema no automatizado
La tarifa horaria del empleado es un valor medio para el salario total / costes salariales de los empleados. Ya tiene en cuenta los costes relacionados con los salarios. Debido a la operación de turno único, no se realiza ningún permiso de turno. Se asume una disponibilidad del sistema del 90%. Debido al tamaño y el equipamiento de los sistemas, se espera un factor de mantenimiento de 0,05. En este caso, los costes unitarios de la máquina se calculan sobre la base del número especificado de unidades y no con la salida máxima posible de la unidad.
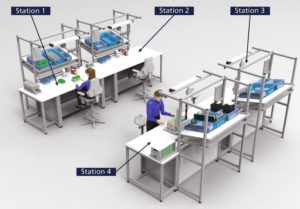
El nivel básico dispensa la automatización debido a la baja producción ya los bajos costos de inversión. Para aumentar la producción, se proporcionarán empleos adicionales para el exceso de capacidad. El diseño final del nivel básico se puede ver en la figura al lado.
El área de la fábrica es de 50 m² con una inversión de 80.000 euros. Los costes de inversión consistía en los costes para las cuatro tablas de trabajo de € 7.500 cada uno y otros gastos menores para los destornilladores, sistemas de soldadura simple y otros, totalizando € 50.000.

En total, un máximo de 1.770 módulos y 13.563 bloques de células al año pueden ser producidos con dos empleados. Con el aumento de la demanda, el volumen de producción se puede aumentar a 27.148 bloques de células y 3290 módulos con la ayuda de dos empleados adicionales. En esta fase, se consumen cerca de 2 kWh de electricidad por hora. Los costes de montaje son de 236 euros por pieza. El período de retorno es de 18,73 años.
Etapa 1: sistema de robot pequeño se integra
En la etapa de expansión 1, todos los recursos del nivel básico se pueden reutilizar. Esto reduce los costos de inversión en comparación con una nueva inversión y el esfuerzo para reconstruir el sistema. Para el cálculo, sin embargo, la inversión total se calcula para obtener valores comparables. La inversión total es de 157.000 euros con un período de retorno de 0,41 años.
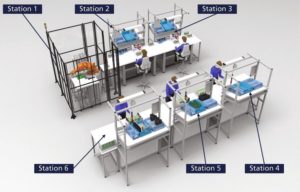
Además de los costos del nivel básico, una mesa de trabajo adicional cuesta costos de inversión de 7500 euros y 75.000 euros para el sistema de robot pequeño. El robot aumenta el consumo de energía a 5 kWh. La planta tiene un área de exigencia de 60 m². La fábrica puede producir un máximo de 4631 módulos y 40.723 bloques de células al año, con cinco empleados. Un aumento en la producción sólo es posible aumentando las horas de operación. Los costes de montaje son 143 euros. El diseño de la etapa de expansión 1 se muestra en la figura al lado.

La tabla adyacente muestra los valores de cálculo individuales. La comparación de los dos sistemas muestra que la primera etapa de desarrollo ya se amortizó después de un año con los mismos costes de instalación de 240 euros por pieza. El ejemplo muestra la importancia de los datos de entrada de las instalaciones para la comparación. Para una mirada más atenta, recomendamos una mirada en el libro «Industrierobotik«.
* Autores: Prof. Dr.-Ing. Gunther Reinhart, Dipl.-Ing. Alejandro Magaña Flores, Dipl.-Ing. Carola Zwicker
* [1] Warnecke, HJ; Bullinger H.-J. Hichert, R; Voegele, A.: Contabilidad de costes para ingenieros, 5ª edición. Múnich: Hanser Verlag.
* [2] Jovesz, W .: cálculo de costo e inguinal. Stuttgart: Schässer-Poeschel-Verlag, 4ª edición.
* [3] Wöhe, G: Introducción a la Administración General de Empresas, 23ª edición. Múnich: Editora Franz Vahlen.
Articulo relacionado: Cuántos trabajos reemplazan realmente los robots?
Dejar una contestacion